Blended Program: Converting Operators to New Process Automation Control System
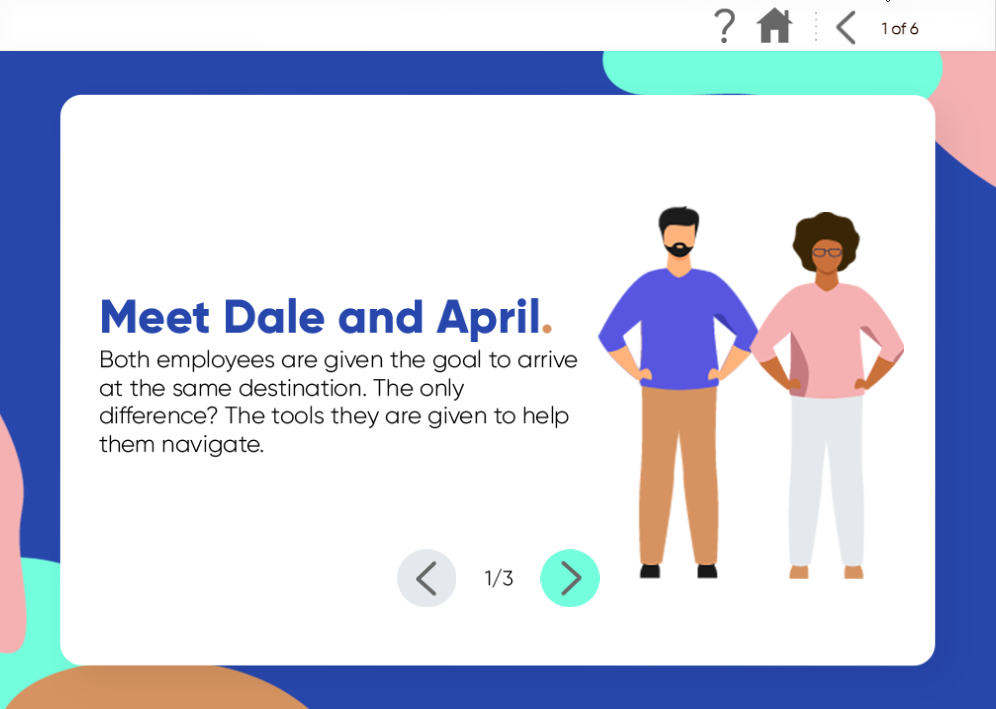

Make it simple, as simple as possible.
For this project our challenge was to build training to introduce manufacturing facilities to a new process automation system and give the operators the training that they need to become experts on running their facilities safely and efficiently. While the new state of the art technology and system is much more streamlined than the system previously used, running a chemical plant from a computer is no easy feat.
To make it happen I designed a 4 phase approach:
Phase 1: eLearning Series
We wanted to start the training off with small simple wins to build the learner’s confidence, so we created eight 15 minute eLearning modules complete with costume graphics, videos, and interactions. Each module strips away as much detail and complexity as possible to help learners understand how things work together on a macro level.
Phase 2: Generic Simulator Training and Self Paced Practice
In this phase we provided employees 1:1 time with the new system. on a generic simplified plant simulation. Our intention was to provide a list of objectives/tasks and provide a binder of job aids that they could work through and practice with in their spare time.
Phase 3: Facility Specific Simulator Training
For phase 3 we transitioned to a learning experience that would more closely mirror what they would see in their plant day to day.
Phase 4: Assessment and Certification Requirements
In phase four we evaluated their knowledge and skills, and set up requirements (job shadow, supervised work, etc) to sign off on their ability to operate their plants.